Silver/copper pressure sintering is a heat-treatment process applied to a powder material which is currently considered the most reliable technology for connecting components in power electronics.
From “Editorial Staff”: https://www.powerelectronicsnews.com/author/editorial-staff/Technology is evolving more and more. The industrial sectors follow the evolution and companies focus on the most requested applications in the market, changing their focal point of production, according to the needs of consumers. AMX invented a novel sintering tool for their sintering press, the Micro-Punch, which can press each component on the substrate independently and with a specific pressure (thermistor, IGBT, MOSFET, die, chip). The AMX Micro-Punch tool ensures uniform pressure and, most importantly, eliminates the following high-value issues: die fracture, tilting, delamination, and voids. The Micro-Punch tool has no restrictions on the number of dies or their placement; it can adapt to any DBC size or configuration, and it can press the thinnest and tiniest dies independently, even if they are quite near to one another.
Pressure sintering
Silver (Ag)/copper (Cu) pressure sintering (see Figure 1) is a heat-treatment process applied to a powder material, namely nanoparticles, to give greater strength, integrity, and conductivity. Sintering is currently considered the most reliable technology for connecting components in power electronics. Silver-sintering paste is currently the most widely used material. The melting point is about 960°C and the thermal conductivity of a silver-sintered paste is between 130 and 250 W/(m⋅K). The silver-sintered paste has a high adhesion of the epoxy resin, keeps the components in a fixed position for their excellent management, and, in general, increases the total yield of the process. The next generation entails copper sintering, particularly to achieve significant cost savings. When compared with other bonding methods, pressure sintering has several advantages:- It has the best thermal conductivity coefficient (>150 W/(m⋅K)).
- It has the best electrical conductivity coefficient.
- It provides best results on durability tests, even 100× better than welded interconnections.
- It shows high re-melting temperature (>400°C).
According to AMX, its patented pressure-sintering technology allows:
- Sintering of silicon and silicon carbide on DBC/AMC and other plated substrates or bare copper
- Frame/discrete
- Embedded dies, clips, spacers, etc.
- Interaction of different materials, surfaces, and processes
The new applications include multi-level interconnections, integrated modules, component joining, electrical distribution, UPS transformation and storage, charging stations, inverters, servomotors, radars, and sensors.
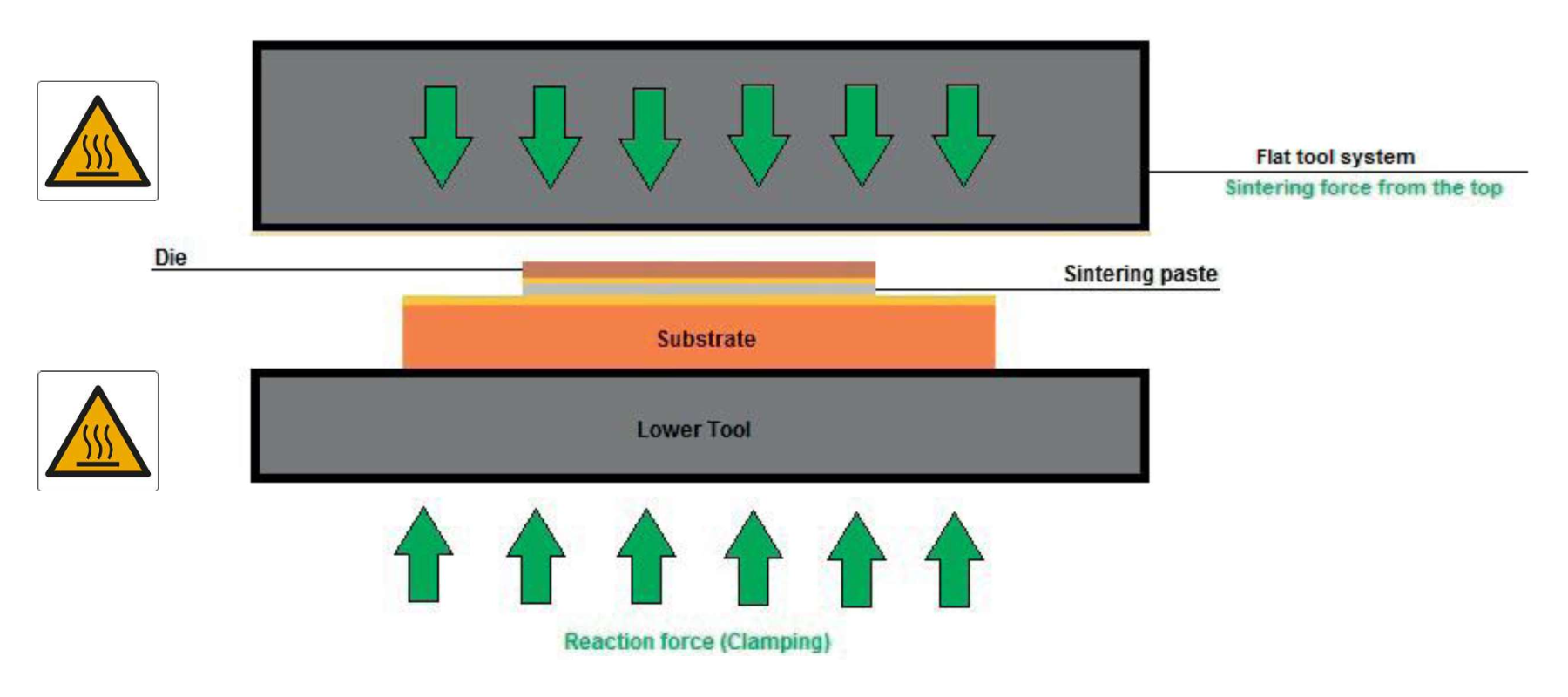
A new method: the Micro-Punch
During the research, the company patented an innovation that obtains the best results from the sintering processes, as shown in Figure 2. This is the Micro-Punch system, which is completely different from the traditional system and represents a significant advancement over what was previously used. The first system was made up of a single presser that applied the same force to all components. Any difference in thickness of the various components inevitably entailed problems. In other words, if on a certain point the layer of dough was a little thicker, all the force of the pressers was applied precisely on that point, multiplying the pressure out of all proportion and increasing the risk of breaking the materials.The company has introduced a significant innovation with the Micro-Punch system: Pressure is now applied independently on each single point, using a dedicated presser. As a result, the previous issue is eliminated. Alessio Greci, sales manager at AMX, said, “The AMX patent has totally innovated this production sector and the AMX system is, undoubtedly, much more advanced. It focuses above all on the quality of the final result. The competition has developed some intermediate and alternative solutions, usually grouping several pressors into subgroups, but MicroPunch system show outstanding results in terms of repeatability and especially in advanced package application, despite the fact that cost of ownership and the processing times are the same.”
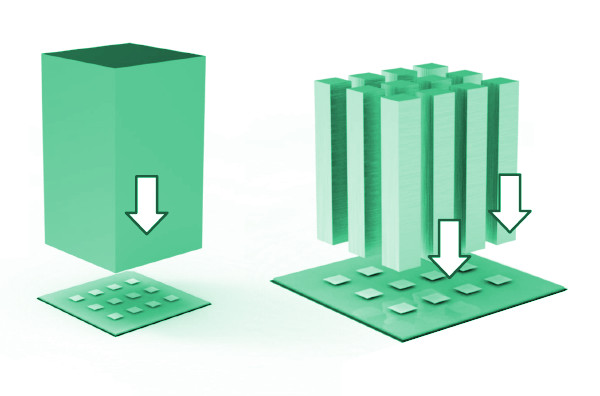
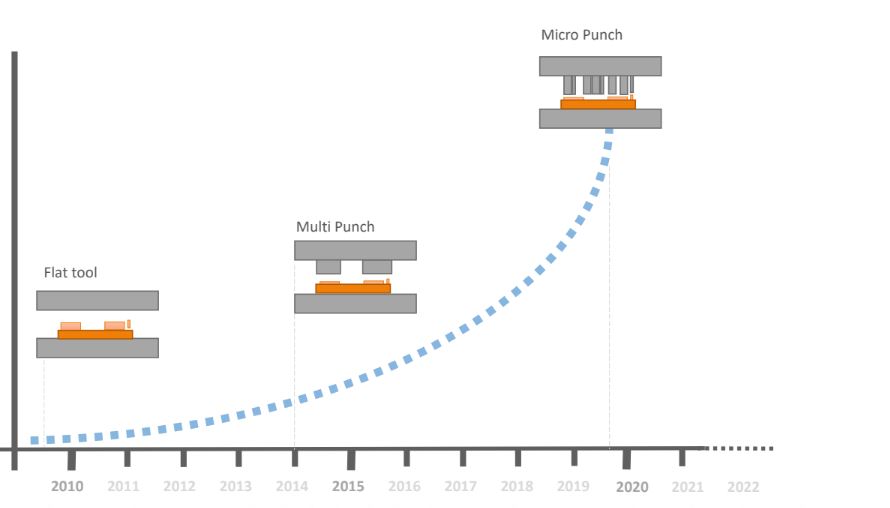
Maximum customization
The Micro-Punch system is highly customizable to meet the needs of the customer. Many of them, in fact, are more concerned with the solution’s accuracy and dependability than with its cost. The elimination of material breakage issues is a primary requirement. It is eliminated by the AMX method, and there is no longer any phenomenon of breakage or deformation. This requirement is felt most acutely when various types of electronic components are involved in the process, such as a mix of diodes, MOSFETs, and thermistors. It is now very simple to combine 130-µ and 400-µ components. With the Micro-Punch, each presser is dedicated to a single point (see Figure 4), and the entire system is capable of independently pressing the thermistors as well as the IGBTs.Furthermore, the Micro-Punch can apply different and independent pressures to the various electronic components. In this manner, the customer can apply slightly less pressure if they believe the component is more brittle and does not respond well to high pressure. As a result, during the design phase and in accordance with the customer’s specifications, it is possible to select between different pressures and which components to apply. As a result, the machine that is ultimately produced is completely customized to meet the needs of the end user. A pressure ratio between the various pistons, for example, can be defined, specifying a parameter that identifies that a piston must press twice as much as another piston.
“Obviously these parameters, which were initially chosen, can be modified by the customer every time the circuits change, and [they] can modify, from time to time, the relationships between the pressures that are applied,” said Greci. The Micro-Punch system can handle elements that are extremely close to each other, as the components can theoretically have a GAP equal to zero and touch each other while being free to move. Sintering is currently used in semiconductor applications such as SiC.
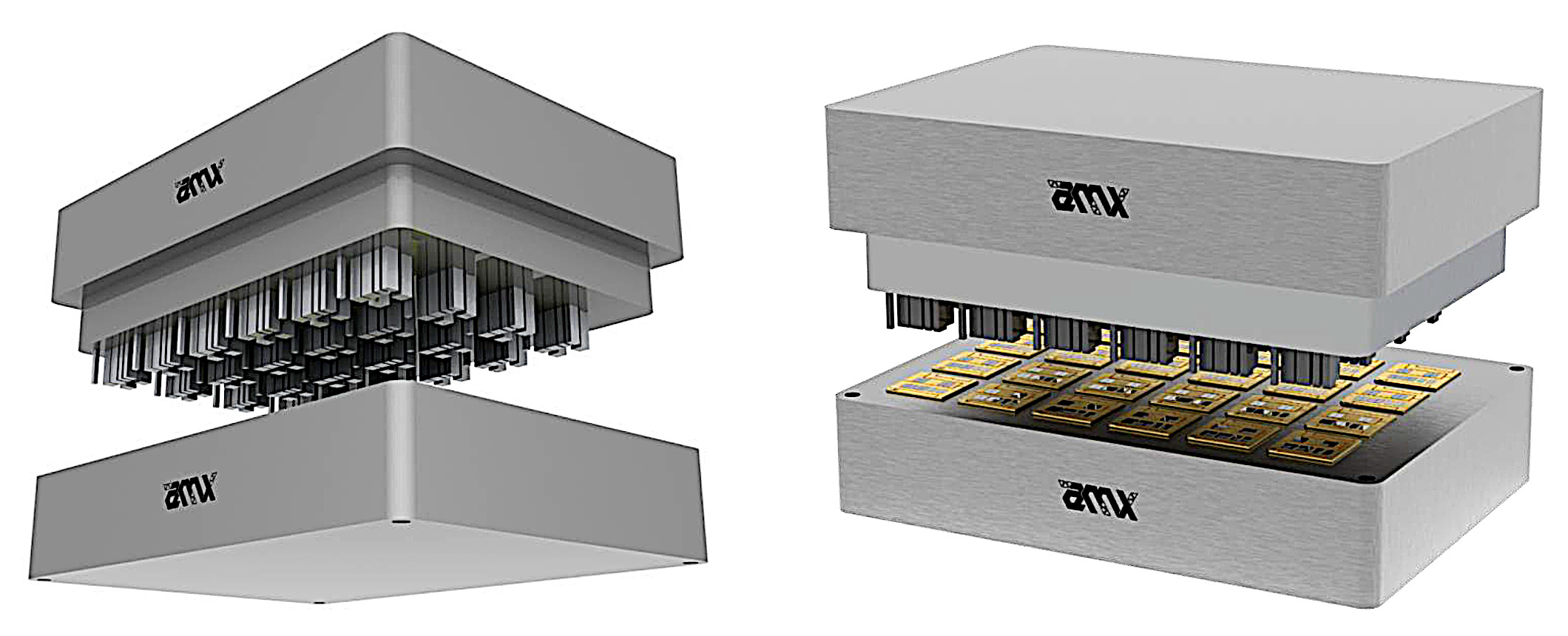
Sintering in the automotive sector
In the past years, everything was welded together in cars. AMX is also implementing pressure-sintering methods in the automotive sector, especially for very high-power modules. Today, the market requires greater miniaturization along with high power, and most of the company’s activities will be focused on precisely this type of application. There are also implementations for public transport with trains, but they obviously have fewer space problems. In fact, miniaturization mainly concerns the automotive sector. Other applications of power modules also involve data centers, uninterruptible power supplies, and large power transformers.Pressure sintering: a set of important parameters
The difference between the various sintering procedures is determined not so much by the type of component to be sintered as it is by the paste that is selected and used. The customer can select both the paste and the working process to be followed. There are obviously some initial parameters that are chosen a priori, which are more or less standard. The sintering process necessitates a temperature of about 250°C, a pressure of 15 to 25 megapascals, and a time of about three minutes. This is the starting point for describing an entire process.Following the initial results, it is possible to tweak some parameters to achieve the best possible outcome. Typically, the customer examines the effects of force or thermal ones, observing the component’s reaction to various types of fatigue and analyzing the various parts under a microscope. Typically, these parameters are set by the paste manufacturers and fine tuned during trials process by process. Finally, pressure sintering is a process that allows for high temperature sealing with high reliability, perfect repeatability and it is currently regarded as the best solution. Other parameters, such as temperature and the coefficient of thermal expansion, must be evaluated.
The double feedback system
AMX offers the “double feedback” option. This is an extremely important feature that avoids errors in applying pressure to components. The pressure applied on two fronts is controlled:- On the pressers
- On the specific point on which the force is exerted
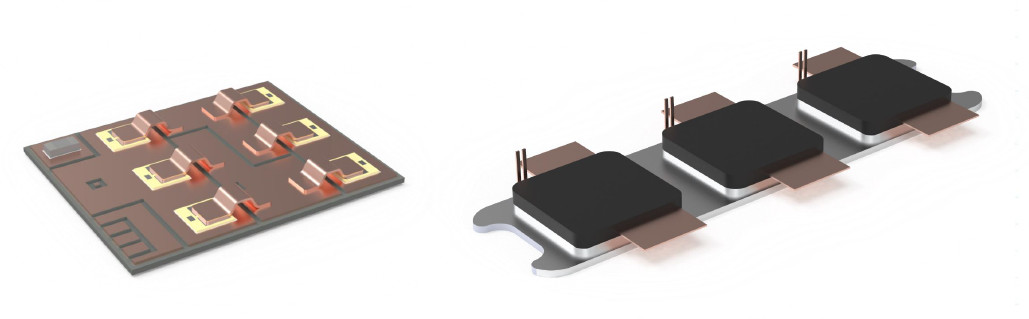